Harvey Mudd College, Scott A. McGregor Computer Science Center
Claremont, California
BEST PROJECT
KEY PLAYERS
OWNER:Harvey Mudd College
LEAD DESIGN FIRM:Steinberg Hart
GENERAL CONTRACTOR | CONSTRUCTION MANAGER:DPR建设
CIVIL ENGINEER:Kimley-Horn
STRUCTURAL ENGINEER:Brandow & Johnston
MECHANICAL AND PLUMBING ENGINEER:ACCO Engineered Systems
LANDSCAPE ARCHITECT:LandLAB
SUBCONTRACTORS:CSI Electrical Contractors; Lunstrum Windows; GES Sheet Metal Inc.
The three-story, 36,000-sq-ft academic building provides a much needed new home for the college’s growing computer science department as well as a permanent makerspace. Unlike traditional campus structures, the building is a physical embodiment of the college’s forward-looking culture.
Related link: ENR California Best Projects 2021
(Subscription Required)
A unique skin, which makes up about 70% of the building exterior, was the product of creativity, collaboration and target value design. Rather than installing a premanufactured rainscreen system, the project team adapted standard sheet metal to develop a formed panel system, segmented into 6-in. unitized sections and built frame. Along with achieving a distinctive, yet cost-effective look, the custom rainscreen system reduced the construction schedule by four months and helped bring the project into budget.
To balance costs with efficiency, the team blended two mechanical systems for the single building. The traditional chilled water system for the teaching lab spaces is supplemented by a variable refrigerant flow system in the offices. The hybrid system reduced overall energy consumption by balancing the utilization of the existing central plant and the project’s intended use.
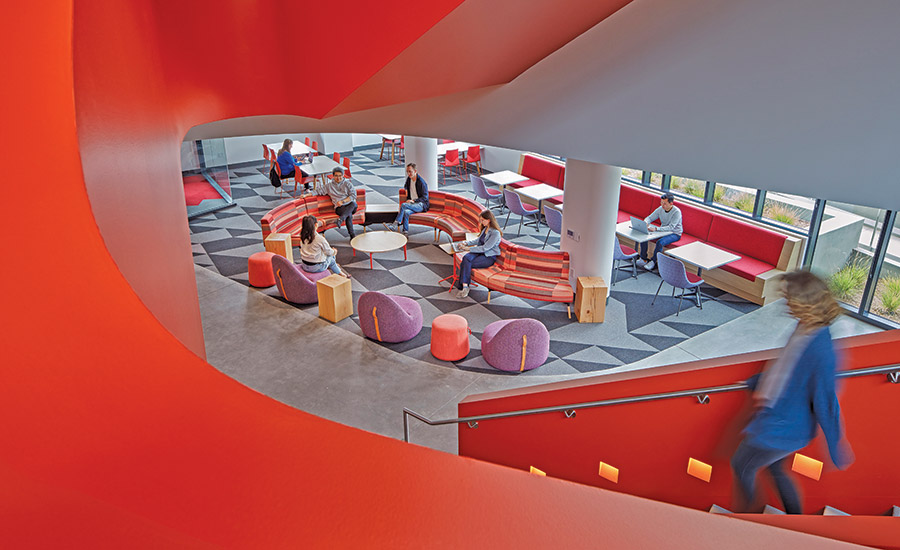
Photo credit: Gensler/Ryan Gobuty
Appropriately for a science-focused structure, the project team maximized its use of advanced construction technology tools to address the unconventional angles, tight tolerances and other facets of the building’s unique shape. BIM and VDC technology played an integral role in addressing cantilevers, unusual corners, roof setbacks and other details. At a transition on the west elevation, for example, the metal panel system was in and out of plane. The project team scrutinized joint consistency and plumbness with the building, confirming the detail and accounting for allowable tolerances.
Inside, the main entry stair fans out as it descends, requiring coordination for the foundation, installation and detailing. Laser-scanning the prefabricated curve track and stairs helped ensure that the custom pieces were a perfect fit prior to installation. Technology also helped address surprises in the field, such as the discovery of an undocumented duct bank.